Room for the modular inn
Updated: 2015-01-23 10:37
By Cecily Liu(China Daily Europe)
|
|||||||||||
Firm finds success building modern prefab rooms that are shipped from China to produce hotels in the UK, often for upscale companies
Chinese modular construction techniques are transforming the global construction industry with their environmentally friendly and cost-effective advantages, and leading this wave in the United Kingdom is CIMC Modular Building Systems Ltd.
CIMC MBS is a subsidiary of China International Marine Containers, a Shenzhen-headquartered company founded in 1980. It initially started as a manufacturer of shipping containers, but over the years, expanded into building ships, tank storage facilities and oil rigs, and even financing projects.
The company already has worked on more than 10 projects in the UK, mainly building standard modular units for hotel rooms at its China factory, and then shipping them to construction sites.
Clients include InterContinental Hotels Group, Rezidor Hotel Group, Accor and Hilton. Its first project was the Holiday Inn Express hotel at Gatwick Airport, completed in 2009.
The company says that CIMC MBS, founded in 2004, is the largest provider of modular buildings and modular building systems in the world.
The area that CIMC MBS focuses on is called volumetric modular construction, which means the company ships a box of a certain size to its client and in the box there is a finished room. The rooms are then stacked together to form the final building.
Michael Crane, design manager of CIMC MBS, says modular construction provides about 25 to 30 percent cost savings over conventional construction methods through capital cost savings, time and on-site cost savings.
The capital cost savings is from lower labor and materials costs in China.
Modular construction is especially competitive for buildings around five to seven stories high, or even higher, because the unit costs for the modules are the same, but in conventional construction methods, cost increases with height as the thickness of the steel and concrete frames needs to grow to hold the weight properly, Crane says.
Secondly, less time spent on site for a project also cuts costs because the project needs construction equipment for a shorter period of time.
And finally, the project means a project can start generating revenue earlier. For a 200-bedroom hotel, traditional construction methods take 12 months, but this can be cut to 10 months with modular building, Crane says.
The expansion of CIMC MBS coincides with a large wave of Chinese investment in UK infrastructure. Crane says these investments are providing the company with great business opportunities.
These infrastructure projects include Beijing Construction Engineering Group's investment and participation in the 800 million pound ($1.2 billion; 1.04 billion euros) Manchester Airport City and the 1 billion pound Asian Business Park in London.
Crane says his colleagues in China are already having talks with Chinese groups including BCEG and ABP, and he says he thinks CIMC MBS' understanding of the Chinese and UK markets put it in a good position to negotiate such potential partnerships.
CIMC MBS also has a subsidiary in Perth, Australia, with an operating model similar to that in the UK.
In both places, CIMC MBS has recruited a large number of local employees with lots of expertise in construction. An example is Crane, who previously worked extensively in the hotel sector as a design manager for a building contractor.
"I used all my experiences in building hotels in the traditional way to help clients understand the advantage of the modular construction system. I understand what risks a contractor would be worried about, and made sure our systems would solve all those problems, so the package we propose to clients leaves them little to be nervous about," he says.
In addition to cost advantages, modular construction also provides certainty, quality and reduces risks, Crane says. He says the two largest risks in construction are how to get a project off the ground and how to keep it watertight during construction. Modular units, transported in shipping containers, are guaranteed to be watertight.
Modular building has been popular in the United States since the 1950s. In the UK it has been used since the 1960s but limited in scale and quality.
Since the late 1980s and 1990s, bathrooms have become popular as modular units because they are often the most difficult to construct, with their pipes, tiles and concrete finishing. CIMC MBS has extended the hotel room model to include the whole bedroom.
Crane says there are some UK-based modular construction companies, but they face the challenge of high UK manufacturing costs and a lack of scale for their projects.
"UK factories are modern, high-tech and expensive to run, so the businesses can't afford to have an empty factory for one day because the overhead is huge and they need to continuously generate money. So they limit the number of modules they build each day," says Crane.
That means a UK modular system factory may take a few months to build a 200-bedroom hotel, but even that became difficult when the recession hit and orders dropped.
But CIMC MBS does not face that problem because its factory lines in China mainly focus on shipping containers, so there is continuous work coming in on a large scale, and when a big modular system order is received it can be finished in a short space of time.
CIMC MBS established offices in the UK in 2011 when it acquired the modular system design company Verbus.
Verbus was established in 2005 and has worked with CIMC MBS in transporting modular units. It was hit badly by the recession as clients became conservative and switched to traditional construction.
CIMC MBS saw value in Verbus and felt optimistic about the growth of modular construction in the UK, so it acquired Verbus, which at the time had three employees. The team has grown to 10 staff members, who mainly talk to UK companies and communicate their needs to the Chinese headquarters.
Crane says one big change that has greatly facilitated the company's UK growth is the decision two years ago by CIMC subsidiary CIMC Capital to finance some of the company's projects in Britain.
Before that, CIMC was only a subcontractor in the construction process, dependent on satisfying the requirements of many other parties in the process, including the investor, developer, main contractor and design team.
But by having CIMC Capital become the investor in a project, the company can influence project guidelines to suit its own systems and capabilities. For example, it can make minor adjustments to the scale of a hotel room unit to make the manufacturing or transportation process more suitable for its systems.
Crane says the arrangement with CIMC Capital took a long time to establish because such a model was unprecedented for CIMC Capital and UK hotel groups.
Traditionally, the hotel groups pay for modular units in advance, effectively purchasing the units from CIMC MBS. But if CIMC Capital finances the overall project, it reserves the right to take over the hotel if the hotel cannot successfully pay back the borrowed amount within the agreed timeframe.
Crane says CIMC Capital would do its own due diligence on projects and only invest in projects that made sense financially to the company.
Despite the optimism and advantages of modular construction, Crane says it is still a new field and sometimes clients do not like to be early adopters. Most of their client projects have been in operation for two to three years, but many hotel groups want to see established projects running for five to 10 years.
Meanwhile, a new area Crane's team is exploring is to expand the company's modular construction to Africa in partnership with UK hotel groups. Having a base in London is perfect for this work because London is where many African hotels are financed, he says.
At the Africa Hotel Investment Forum in June in Ethiopia, CIMC MBS worked with Hilton to exhibit a modular hotel room at a reception Hilton hosted the evening before the conference.
"Hilton wanted to show the African investors that if they order a Hilton modular hotel room from CIMC MBS, this is exactly what they would receive, the same room, the same quality, same materials and same standards," Crane says.
cecily.liu@chinadaily.com.cn
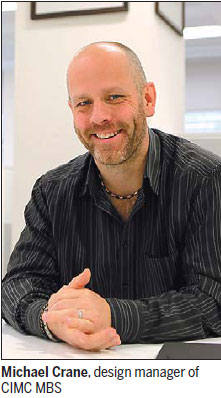
CIMC MBS project in the UK includes the Holiday Inn Express hotel at Gatwick Airport, completed in 2009. Photos Provided to China Daily |
(China Daily European Weekly 01/23/2015 page8)
Today's Top News
China offers Swiss $8b quota for yuan trading
Best team China in decade carries countrymen's hope
Russia says DPRK sent positive signal on Kim visit in May
Australia PM quashes rumours of unrest as 'nonsense'
China aims for stronger links with fragile Europe
China to instill national characteristics in think tanks
Shanghai govt releases report on stampede tragedy
Fake condoms, Viagra, seized and online network shut down
Hot Topics
Lunar probe , China growth forecasts, Emission rules get tougher, China seen through 'colored lens', International board,
Editor's Picks
![]()
|
![]()
|
![]()
|
![]()
|
![]()
|
![]()
|