Tough pill to swallow
Updated: 2011-02-11 10:59
By Li Wenfang (China Daily European Weekly)
A worker reads recruitment advertisements at a labor market in Zhuji, Zhejiang province. Guo Bin / for China Daily |
Increases in minimum Wages force many companies to alter their growth strategies
Rising labor costs coupled with shortage of skilled manpower is eating into the profits of domestic and foreign businesses in the export-oriented Pearl River Delta region of Guangdong province. Labor costs in the region have risen by nearly 20 percent and most of the companies are bracing for more hikes due to an impending increase in the minimum wages, provincial authorities say.
Italian eyewear manufacturer Luxottica Tristar (Dongguan) Optical Co has increased the minimum monthly wages for general workers to 1,000 yuan (111 euros) this year compared with 920 yuan (102 euros) for 2010. The company will make further wage adjustments as and when necessary, says Sam Yang, an executive of Luxottica Tristar (Dongguan) Optical Co.
In Guangdong, where most of the Hong Kong companies have manufacturing bases, minimum wages in various cities have risen sharply. Wages increased by 25.7 percent to 35.6 percent between 2004 and 2008, says a recent report from the Hong Kong Trade Development Council (HKTDC). Last year, minimum wages in Guangdong went up by an average of 21 percent.
Official figures show the average wage in Guangdong increased by 11.4 percent from a year ago in the first nine months of 2010, after increasing by 9 percent in 2009.
Most of the companies admitted there was no respite from the wage spiral. More than 74 percent of the respondents in a recent HKTDC survey said they expected higher labor costs during the fourth quarter of last year.
More than 53 percent of the respondents admitted that the rate hikes were more than 10 percent compared to the past three months, while 31 percent felt the costs would go up by 5 to 10 percent. Even as the wage bill mounts, companies are also going that extra mile to spruce up the overall working and living conditions in a bid to staunch the labor bleeds.
"Most of the companies are improving the living conditions in factory dormitories," says Aimee Ocampo, managing editor of Global Sources, a business-to-business media company.
Zhongshan-based British manufacturing firm Star Prototype China Ltd has individual beds, wardrobes, desks, computers with Internet connection and chairs for its workers in the dormitories.
Improving the living conditions is a one-time investment for most companies whereas basic pay increases would mean recurring monthly costs, Ocampo says.
Most of the European companies in Guangdong, like Luxottica Tristar (Dongguan) Optical Co, say they are not suffering labor shortages due to the higher-than-average pay. On the contrary, it is the lower-end businesses that are feeling the labor pinch.
"With inland regions clocking higher growth rates and creating more job opportunities, there is a tendency for migrant workers to stay closer to their hometowns," the HKTDC report says.
During the first quarter of 2010, especially after Chinese New Year, Guangdong experienced an acute labor shortage of about 1 million employees. Though provincial authorities claim that the situation has improved, the region still faces a shortage of 300,000 to 500,000 employees.
"Labor shortages have become a 'normal' and persistent phenomenon," and pushed up wage bills in the region, says the report.
Most of the more than 1,000 key enterprises in Guangdong are facing labor shortages, says Li Xiangming, deputy director of the provincial economic and information commission.
Nowhere is the situation best exemplified than in the export-oriented manufacturing hub of Dongguan.
Labor demand in Dongguan has risen since the second quarter of 2009, reports from the city's human resources and social security bureau say.
Recorded labor with at least one year of contract totaled 3.332 million at the end of 2009 and 3.475 million at the end of 2010.
More than 94,400 enterprises used the seven major labor markets in Dongguan for recruitment in 2010, 24 percent more than the previous year, for 990,000 workers, up 7 percent.
That compares with the 630,000 people who looked for a job at these markets, a 13.5 percent year-on-year decline.
With nearly 90 percent of the workforce in the manufacturing sector coming from outside Dongguan, the turnover rate is as high as 15 percent during the first quarter every year due to the Chinese New Year holidays. That in turn also leads to a seasonal surge in labor demand.
With solid economic growth expected this year also, labor shortage could worsen after the Chinese New Year, the bureau says.
Businesses like electronics, furniture, garments and toys are the worst hit in terms of labor shortage, says Huang Wei, deputy director of the bureau.
"Earlier, we always had a surplus of general workers and a shortage of technical workers. Judging from the current trend, we will soon be deficient in both categories," says Zhang Mingming, chief of the corporate planning department of Dongguan Zhitong Human Resources Market.
Small- and medium-sized processing companies have also been facing the labor crunch, with more than 60 percent of these companies dependent largely on exports, says Lin Jiang, deputy director of the Center for Studies of Hong Kong, Macao and Pearl River Delta at the Guangzhou-based Sun Yat-sen University.
Lin feels that the labor woes are more for Hong Kong and Taiwan enterprises, while European firms, which mainly serve the Chinese market, are less affected.
Due to the structural imbalance in the labor market in Guangdong since the second half of 2010, most of the enterprises are accepting only short-term orders and hire short-term workers and hence not in a position to expand capacity, Lin says.
Workers are not willing to join such enterprises and hence the labor shortages are more in small- and medium-sized companies.
Some small- and medium-sized companies also forfeited orders due to the appreciating yuan and high raw material costs. Bigger rivals who went on a hiring spree bagged these orders.
Lin expects labor shortages at some small firms to worsen after Chinese New Year, with some migrant workers choosing to stay at home for better opportunities.
Provincial authorities are expected to adjust the minimum wage levels according to the actual situation and the price hikes may come into effect soon, says Ge Guoxing, deputy director of the provincial department of human resources and social security.
Guangdong currently has more than 30 million migrant workers, most of whom were farmers.
Provincial authorities have also stepped in to protect the legal rights of migrant workers and granted the urban hukou, or household registration, through a points-based system, strengthened employment training, and enhanced cooperation with other provinces and regions to attract more migrant workers, he says.
At the same time the authorities are also urging companies, particularly labor-intensive units in the Pearl River Delta region, to shift their production to less developed areas where there is an abundant supply of labor.
Rising labor costs, coupled with marked increases in raw material prices especially for steel, copper, plastics and cotton, power and shipping, are also fueling the inland shift, say sources from the provincial foreign trade department.
After a moderate decline from May to July, global metal prices rose by nearly 23 percent between July and December last year. In early December, the price of oil roughly rose by 35 percent compared to the trough recorded in May 2010. The average price of cotton surged by 85 percent in November compared to the level in July, says the HKTDC report.
The Chinese currency appreciated by 3.01 percent against the US dollar in 2010 and shredded the profits of many Chinese exporters.
China's rapidly rising food prices have also contributed to higher operating costs for manufacturers, as they need to provide dormitories and food to migrant workers in the Pearl River Delta region. Accelerating inflation will also stoke expectations for higher wages, says the HKTDC report.
Most of the Hong Kong manufacturers also faced pressure from overseas buyers last year to cut prices. Faced with massive profit shrinkages, most of the companies are now looking to get overseas buyers share some of the production costs to maintain quality.
In fact, China's export price index, after declining in 2009, started to increase in March 2010 and grew by about 5 percent in October 2010. The decline of US import prices from China was reversed in recent months.
These developments indicate that overseas importers are now beginning to accept higher prices. In a recent HKTDC survey, the percentage of respondents that can pass on at least part of the rising labor costs to overseas buyers increased from 43 percent in the first quarter to 60 percent in the last quarter of 2010.
However, China's competitiveness as a production base is not just in the price alone, but rather in an integrated bundle of factors, such as the quality price ratio of output, delivery lead time as well as flexibility in meeting different order requirements.
The market share of Chinese products in US imports, excluding mineral fuels, increased from 18.8 percent in 2006 to 23 percent in 2009, and to 23.3 percent during the first 10 months of 2010.
The market share of more labor intensive Chinese products, such as garments among US imports, also increased from 37.9 percent in 2009 to 40 percent in the first 10 months of 2010, says the HKTDC report.
Exports from Guangdong grew by 27.3 percent to $406.1 billion (297 billion euros) during the first 11 months of 2010, with those to the 27 countries in the European Union topping $60.47 billion, up 25.2 percent.
Europe is the second biggest export market for Guangdong after Hong Kong, with some of the exports to Hong Kong getting re-exported to European nations.
Zheng Erqi and Luo Yang contributed to this story.
E-paper
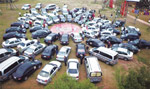
Car sharing helps ease holiday woes
Many car owners offering paid lift services during the Spring Festival rush to reduce their own costs of driving home.
Preview of the coming issue
Global marketplace
Right on cue
Specials
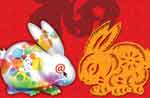
Spring Festival
The Spring Festival is the most important traditional festival for family reunions.
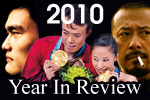
Top 10
A summary of the major events both inside and outside China.
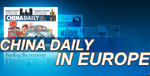
China Daily in Europe
China Daily launched its European weekly on December 3, 2010.